Abstract
The article analyzes features of the process of production management at enterprises in the context of the digital economy. In order to maintain a high competitive level, enterprises are required to respond to changes in the internal or external environments. It is necessary to develop complementary technological processes accompanied by the transformation of resources into public products. This process is referred to as the manufacturing process. The main goal of the digital organization of production is to bring all business activities in line with the rapidly changing requirements of the modern world. For businesses, digital transformation is the overarching process of integrating digital technologies into a new or existing business model. This definition can be applied to other public areas, such as public administration or education. Digital transformation helps businesses to accept even the most radical external changes and remain competitive in the new environment. There is no doubt that it is precisely those states that will be able to create a favorable environment and opportunities for the development, assimilation and wide replication of digital technologies that will set the pace in the world market. Without support for transformations and consolidation of initiatives at the government level, the digitalization of enterprises will remain only one-time successful projects that do not have a significant impact on the overall state of affairs. Competitiveness can be achieved through the use of new production management technologies in the context of the transition to an innovative development path.
Keywords: Digitalization, digital technologies, production management
Introduction
In 2020–2021, the scope of digitalization became wide. This IT infrastructure investment trend will continue its development in 2022. The government will not just automate the processes of state administration, it will become the driving force for the digitalization of the country. Therefore, its dynamics will depend on the economy and on how much the government will be ready to invest in IT.
The fourth industrial revolution has moved from being a predictable future to a very tangible present.
The massive introduction of digital technologies, changed consumer psychology, new market conditions - all this requires changes in production processes and in management. The enterprise of the future is above all an agile enterprise. But the future always grows out of the current moment; it is important, therefore, to understand that the enterprise of the future is a production that has undergone transformations; its business processes have been adapted to the new conditions (Borisova et al., 2020). It is necessary to develop a set of complementary technological processes, accompanied by the transformation of natural resources into public products. This process is referred to as the manufacturing process.
The first group of processes is aimed at realizing the mission of the company. They support the production by transforming resources and raw materials in conjunction with other factors of production. Despite the fact that the main processes are the central element, they cannot support the entire production process without service and support ones.
The second group is intended for the provision of services and the manufacture of goods that are important for the main life of production. It includes production for personal needs of equipment, products, tools; equipment repair; generation of energy, etc.
The third group of processes is associated with the safety of resources and materials, their delivery to the main production, as well as the movement of raw materials within and outside the organization (Novikova & Strogonova, 2020).
The production process takes place in time and space. The proper production management pursues goals such as: reducing the waste of working time, accelerating the turnover of working resources, minimizing costs, and combining the main and auxiliary processes. The characteristic “in time” is measured by the production cycle indicator. It is the period of production of a particular type of goods. This period begins to be measured from the moment of use of natural resources to the final production of products. Its duration depends on many factors (see Figure 01).
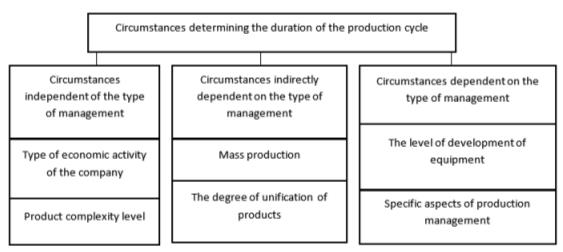
Problem Statement
Factors affecting the duration of the production cycle depend on the technological process.
The production cycle consists of two elements: working hours and breaks.
The working period includes the time spent on the main, auxiliary and maintenance processes. It contains components such as:
1. Time of natural processes. This is the time that is spent on consistent and regular changes in systems, leading to the appearance of new properties, without the direct participation of humans (growth of seedlings, cooling of heated objects). Artificial conditions can be created to speed up the time of natural processes.
2. Time spent on the technological processes. This is the time during which the object of labor changes through the impact by the worker or automated mechanisms.
3. Time of control processes. They must be implemented simultaneously with the technological process of manufacturing the part and assembling the devices.
4. Time of transportation is associated with the transportation of natural resources and finished products to their final destination.
Breaks are periods during which there is no impact on the object of labor and no changes are made. There are two types of breaks: regulated and unregulated.
The duration of the production cycle is calculated based on the time spent on the production of both the entire product and its individual components. Time spent on the production may exceed the time of production of goods themselves, since many elements are manufactured at different places in parallel.
A few years ago, the term "digital manufacturing" began to be used. It was defined as an enterprise that uses automated systems at the stages of production and preparation (Serenkov et al., 2015).
The emphasis was on software that speeds up and simplifies the development, configuration, and operation of application programs for controlling individual machines.
The term is now understood as a digital production process that involves not only the use of technology to increase the productivity of a conveyor line machine. It is the process of creating a digital “twin” for a product or process, or even the entire enterprise.
For example, before starting the transformation of an iron blank into a metal product, a copy is created in the virtual world, which goes through all the stages of production. At the same time, it is possible to see all the difficulties and costs. In the same way, models of a conveyor assembly or an enterprise as a whole are developed.
Digital production models (“digital twins”) are multi-level layouts of both technological and production processes, as well as individual technological operations; they operate with a huge number of production facilities (equipment, employee workplaces, service departments, etc.). The models require accounting and analysis of a huge amount of heterogeneous data. This is one of the reasons why digital manufacturing requires technologies (Idigova et al., 2019).
The use of advanced technological solutions in the production can ensure the development of an enterprise, enhance its image and reputation, and become a major competitive advantage in a world where the consumer needs high quality products.
Research Questions
The main part of the production process occurs at a workshop. It is an independent administrative unit. There are main, auxiliary, auxiliary and secondary workshops.
In the main workshops, goods intended for sale are manufactured.
Auxiliary workshops can be of model, repair, transport, tool types.
Ancillary workshops pack and preserve goods, load and deliver them to the client.
The side shops process and dispose of waste.
There are also non-production workshops that serve non-industrial sectors.
Research and development departments also play an important role in the oil and gas industry. It is here the connection between science and production is visible (Serenkov et al., 2018).
The most important elements of the structure are the main and auxiliary production sites. Specific technological works are performed at technological type sites. Auxiliary units are formed according to the same type as the main ones.
The production management methods are a set of techniques used for the most effective combination of the main components of the production process in time and space.
They can be divided into the following ones: individual and small-scale production, large-scale and mass production, and synchronized production.
The method of individual production is used for manufacturing a single product. It involves
1. use of multifunctional tools;
2. Distribution into groups depending on the intended use;
3. Lack of job distribution;
4. Staged transportation of products from place to place in batches.
Employees use one set of items and a small part of multifunctional tools, which sometimes need to be repaired or replaced due to wear and tear. During the day, products are brought to the workers and taken already processed. Therefore, it is necessary to create effective transport links.
The method of large-scale and mass production is aimed at the production of parts of the same name and is based on the following principles:
1. Each workplace is focused on the performance of a specific task;
2. Careful study of the process of operational maintenance of workplaces;
3. Moving tools one by one or in small batches upon completion of the task;
4. Uniform release of goods;
5. Location of jobs along the technological process.
This method can be used if the following conditions are observed:
1. The production mechanism is technological, each product is mobile and can be divided into structural parts;
2. Individual units of products are continuously supplied, and the time spent on various activities can be clearly identified;
3. The scale of production is at a high level and lasts quite a long time.
The synchronized production method. The fundamental ideas of this method were laid down by the Japanese company "Toyota". It combines several functions: the product quality management system, the tactical planning system and the inventory management system. The synchronized production method aims to stop the production of goods in large quantities and develop continuous production, during which, at all stages, the necessary units are delivered to the place for performing further tasks.
All enterprises are an association of people who pursue similar goals. Organizations have similar elements: management, control, resource provision, distribution of responsibilities, dependence on the environment. The management performs the following tasks: coordination and control, motivation and stimulation, forecasting and planning. They are necessary to achieve goals. Management is considered as a condition for exercising the ownership right. The central link in this process is experts who are the backbone of every enterprise. From this point of view, management is the ability of specialists to achieve the goals by regulating activities, mental abilities and motivation of the personnel.
Al companies are considered as open systems, i.e. they are in contact with the environment. In case of the proper management, an additional cost of resources appears at the input and a large number of positive outcomes appear at the output (expanded range of goods, increasing profits and number of customers).
The success depends on the strategy selected. A strategy is a specific plan of action to the company and achieve its goals.
There are four basic business strategies:
1. The downsizing strategy is applied when the company needs modernization after recession due to changing conditions in the economic, political, social and other areas.
2. The strategy of concentrated growth. Company’s activities are aimed at improving the quality of goods, producing new ones and improving their position in the market.
3. The integrated growth strategy. It aims at tightening control over suppliers, systems between the enterprise and the consumer, as well as at creating branches and subsidiaries.
4. The diversified growth strategy is implemented by looking for opportunities to produce new products using modern technologies in the market and new products that are not related to the old industry.
The organizational structure of management is a set of management decisions, methods and actions aimed at ensuring the implementation of company's functions (improving the structure, distributing responsibilities, powers, duties and tasks among departments, determining the order of interactions). It includes the following components: performers, managers, departments. There are vertical and horizontal links between them.
Vertical links represent a pyramid of management, where orders go from top to bottom, are mandatory and not subject to discussion or revision. Horizontal links exist between structural units of the same level.
These relationships are either linear or functional. The linear nature is manifested in the fact that only line managers who are fully responsible for their departments take part in making decisions.
Thus, all the components are of equal importance for the effective production management, and the role of individual components should not be exaggerated.
Purpose of the Study
The aim of the study is to analyze problems and prospects of digitalization in the field of production management. To achieve this goal, it is necessary to solve a number of tasks:
- to substantiate the relevance of digitalization of production management;
- to identify the main problems in the production management system;
- to assess the level of application of digital technologies;
- to analyze the level of application of digital technologies in the production management system
Research Methods
The study used the methods of statistical and comparative analysess, as well as the methods of expert assessments, which made it possible to identify the main problems in the digitalization of the production management system.
Findings
The digital format involves the automation of processes, which will help speed up the processing of incoming requests and increase the likelihood of receiving orders. Company executives ask reasonable questions: what processes can be automated, what software solutions can be used to implement the standards? Some of the tasks can be solved with the help of products that are used by the enterprise if it is planning to digitalize the production management system (Idigova & Rakhimova, 2021).
The application of this concept helps to obtain benefits the following benefits:
- Growth of productivity due to the efficient use of each unit of equipment, resources.
- Reduction of the percentage of defects.
- Cost reduction.
When designing a product, it is possible to increase the accuracy of all production processes, and this ensures an exact match between expectation and result.
If we are talking about creating a plant or field from scratch, then digital modeling can reduce the final costs. Before you install new equipment or try new materials, there is an opportunity to experiment with "digital twins". This experiment will not cost anything, while real experiments are often costly. It may even prevent management from experimenting, although the results could give the company new benefits.
The accurate mathematical model anticipates any real processes and makes it possible to calculate both the costs and the effectiveness of planned changes.
3D modeling is in demand. In addition to high accuracy, it can save on model development. With the help of computer graphics, enterprises are moving away from long preliminary approvals, thick documents with specifications of the future product.
Product Lifecycle Management is another technology that is gaining momentum. The life cycle starts with modeling and ends with disposal. Constant monitoring of the state of the product (for example, a machine element) at all stages is the key to timely repair or replacement of worn parts. This means that the machine will eventually work smoothly, and if it is part of the conveyor, it will not slow down the operation of the entire line with its failures.
This example reveals one of the important elements of the concept of digital production. Constant monitoring helps prevent breakdowns of production lines, leakage of aggressive liquids and losses caused by force majeure.
There are dozens of other technologies that can be implemented within this concept. But they have the same nature: collection and processing of data obtained from various systems; modeling; automation (reducing the role of a person).
Conclusion
In order to optimize the production management system, it is necessary to evaluate the following types of services: technological maintenance of facilities; construction of production facilities; capital repair; engineering servicing.
The current economic environment is unstable. The sustainable development of enterprises depends on their ability to predict and respond flexibly to changing conditions of the external environment, to retain and acquire new competitive advantages.
References
Borisova, V. V., Tasueva, T. S., & Rakhimova, B. K. (2020). State support for digital logistics. In: Lecture notes in networks and systems.
Idigova, L. M., & Rakhimova, B. K. (2021). Current issues of digital transformation of the oil and gas industry. In: Problems of the economy and management of the oil and gas complex.
Idigova, L. M., Tagaev, C. K., Tasueva, T. S., Israilov, M. V., & Magomadov, E. M. (2019). Modernization of regional industry on the threshold of digital economy. Social and cultural transformations in the context of modern globalism (pp. 2158–2166). Groznyi: Russian Acad. Sci., Complex Res. Inst. Kh.I. Ibragimov.
Novikova, N. V., & Strogonova, E. V. (2020). Regional aspects of studying the digital economy in the system of economic growth drivers. Journal of new economy, 76–93.
Serenkov, P. S., Kuryan, A. G., & Volontey, V. P. (2018). Methods of quality management. Process approach. Infra-M.
Serenkov, P. S., Gurevich, V. L., & Romanchak, V. M. (2015). Methods of quality management. Methodology councils. Infra-M.
Copyright information
This work is licensed under a Creative Commons Attribution-NonCommercial-NoDerivatives 4.0 International License.
About this article
Publication Date
25 November 2022
Article Doi
eBook ISBN
978-1-80296-127-0
Publisher
European Publisher
Volume
128
Print ISBN (optional)
-
Edition Number
1st Edition
Pages
1-742
Subjects
Sociolinguistics, linguistics, semantics, discourse analysis, translation, interpretation
Cite this article as:
Idigova, L. M., Plis, S. A., & Chaplaev, H. G. (2022). Production Management Problems In The Digital Sphere. In D. Bataev, S. A. Gapurov, A. D. Osmaev, V. K. Akaev, L. M. Idigova, M. R. Ovhadov, A. R. Salgiriev, & M. M. Betilmerzaeva (Eds.), Social and Cultural Transformations in the Context of Modern Globalism (SCTCMG 2022), vol 128. European Proceedings of Social and Behavioural Sciences (pp. 303-309). European Publisher. https://doi.org/10.15405/epsbs.2022.11.42