Abstract
This paper examines the organizational features concerning the implementation of digital technologies in mechanical engineering production. When introducing advanced technologies into the production process, the main attention is usually paid to technical aspects, and insufficient attention is paid to organizational and economic aspects. The authors show that organizational factors are no less important than technical ones because they can generate transaction costs, the amount of which can level the economic effect caused by the introduction of new technologies. The machine-building production development testifies that together with technical innovations, organizational innovations were created, which contributed to the disclosure of the potential available for new technologies in the production system. By the example of machine-building enterprises, it is shown, that ignoring the organizational factors reduces the efficiency of modern digital technologies and requires additional costs for their implementation. A comprehensive approach to the implementation of advanced digital technologies is necessary to avoid unnecessary costs and to increase the efficiency of their use.
Keywords: Digital technologies, mechanical engineering production, organizational factors, technology, transaction costs
Introduction
At present, there is a radical technological basis transformation of modern machine-building production through the introduction of digital technologies. New technologies contain a significant potential for increasing labour productivity, the realization of which provides a sustainable competitive advantage. For the Russian machine-building industry, modernization of production systems based on digital technologies is a key direction of transition to the non-resource scenario of economic development and provision of technological independence of the country.
In the last decade, in Russia measures for technological modernization of machine-building industries have been implemented, significant resources are invested in the creation of new products and technologies of their production, the material and technical base of enterprises is updated. This allowed increasing the share of the high-tech machine-building sector in the country's economy: at present, the machine-building sector accounts for 2.5% of the added value created in the economy.
Problem Statement
The issues of organizing production processes in mechanical engineering were considered in the works of domestic and foreign researchers such as Fayol et al. (1992), Sokolitsyn and Kuzin (1988), Novitsky (2002) and Fatkhutdinov (2005). A comprehensive approach to the study of technological development problems is presented in the works by Perez (2011), Glazyev (2010) and Sukharev (2008). The influence of digital technology on modern product development is devoted to the works by Brynolfson and Makafi (2017), Ford (2016), Astakhova et al. (2019), Shashlo et al. (2019), etc. The role of organizational factors in production systems development is studied by Titova (2020), Christensen and Overdorf (2000), Williamson (1996), Yakubovsky (2006), Danchikov et al. (2017), Kuzubov et al. (2018). However, the available works do not pay enough attention to the problems of implementing digital technologies in machine-building production, which requires additional research.
But despite positive shifts in the development of the industry, the share of high-tech machine-building products does not cover the internal needs of the country: machine-building products account for 44.5% of Russian imports. One of the reasons constraining the technological development of domestic mechanical engineering is insufficient attention to organizational factors when carrying out measures of technological modernization, which determines the need for further research.
Research Questions
The main issues of the study: the study of organizational factors of technological development, the identification of problems of implementing digital technologies into machine-building production.
Purpose of the Studу
The purpose of this work is to investigate the role of organizational factors in the implementation of digital technology in machine-building production.
Research Methods
The main methods of research can include the method of observation (determination of working time losses), economic-statistical method, and logical reasoning.
Findings
1. Organizational factors of technological development.
The existing approaches to the understanding of technological development are focused on improving the production system through the development and implementation of technological innovations. At the same time, insufficient attention is paid to the organizational component of technological development, which does not allow revealing the potential of new production technologies.
Production and distribution of products within the production system involve the intersection of related technological stages. From the technological point of view, the transition of products from one stage to another is not associated with significant resource costs and should be carried out without hindrance. However, apart from the technological system, the production one includes the economic and social components based on informal relations. Therefore, in addition to transforming the technological structure of the production system, the introduction of new technology affects the socio-economic relations between the participants involved in the production process. This can lead to the emergence of barriers in implementing the new technology; to overcome the barriers, it will be necessary to spend significant resources, which will increase the cost of products and reduce their quality. To avoid this, it is necessary to take into account economic and social aspects in the designing of the production process.
In the economic theory of organizations, a transition of products from one production stage to another is called "transaction" (Williamson, 1996, p. 27). The advancement of goods along the technological and distribution chains will be effective if we create structures that coordinate the activities of subjects involved in the process of production and sale of goods. The creation and operation of the transaction management structure involve resource consumption, which represents transaction costs. There are market and management transaction costs (Perez, 2011).
Market transaction costs arise during the conclusion and implementation of market transactions. They include (Odintsova, 2009):
- Costs for finding a partner and the costs of collecting information about the product offer;
- Costs for negotiating and decision-making (negotiation of contract terms, the conclusion of a contract, collecting additional information, engaging consultants, etc.);
- Costs for monitoring and enforcement of a contract (tracking delivery time, measuring the quality of delivered goods, forcing the counterparty to comply with the concluded contract, etc.).
Management transaction costs are inherent in hierarchical management systems, and include (Furubotn & Richter, 2005):
- Costs for creating, maintaining or changing the organizational structure;
- Information costs (the costs for making management decisions, monitoring the execution of orders, evaluating the performance of employees, etc.);
- Costs associated with the physical movement of goods and services within the boundaries of related production processes (the cost of moving objects of labour within the enterprise).
Transactions of a certain type correspond to the management structures that take into account their characteristics, which allow minimizing transaction costs. Williamson (1996) includes the specificity of assets (the specificity of "human capital", fixed assets, location, as well as target assets) to main characteristics of transactions. Asset specificity implies making investments in assets that can be used in a certain type of activity. Alternative use of specific assets is associated with large losses of invested funds. The emergence of specific assets is caused by the development of scientific and technological progress. This leads to the fact that organizational innovations should be carried out together with technical innovations to minimize transaction costs. The development of mechanical engineering technology confirms this thesis.
The emergence of mechanical engineering dates back to the beginning of the twentieth century when technologies for the production of internal combustion engines and electric motors, technologies for obtaining synthetic materials and also fuels were created. Production during this period has become high-volume. To unlock the potential of new technologies, the Taylor-Ford system of production organization was developed. The main provisions of this system are (Fayol et al., 1992; Volkov & Devyatkin, 2010):
- Division of the production process into elementary components - labour movements, the study of the cost of working time to carry out these movements, determination of optimal movements;
- Designing the production process based on optimal ways of performing work, which made it possible to use workers with low qualifications;
- Ensuring full interchangeability of parts and units of a manufactured product, which made it possible to organize their flow production;
- The use of conveyor, to ensure the continuity of production processes;
- Standardization of the production process, including raw materials in use, consumables, equipment, and technological processes;
- Separation of design functions (product design and technology development) from fulfilment functions (product manufacturing), which allowed to scale production.
The second stage in the development of mechanical engineering is associated with the emergence of automated systems, which allowed increasing labour productivity and flexibility of production systems. Unlocking the new technology potential was allowed due to the lean production system presupposing the involvement of personnel in solving the problems that arise with the help of various organizational tools: "quality circles", "kaizen", etc. (Womack, 2003).
At present, mechanical engineering enterprises are in a state of transition to new technologies, the core of which will be digital technologies. The most promising digital technologies in mechanical engineering include the following (Brovko & Petruk, 2016; Brynolfson & Makafi, 2017; Petruk & Shashlo, 2019; Petruk & Vorozhbit, 2017; Shashlo, et al., 2018, Titova & Terentyeva, 2020):
- Computer engineering - a set of software products used for product design (CAD-systems), engineering analysis (CAE-systems) and production (CAM-systems), and also including cloud computing and big data processing technologies;
- Additive manufacturing - manufacturing products based on three-dimensional computer models by layer-by-layer deposition of material in special machines;
- Robotics - the use of robots to perform basic production operations, control the production process, and transport;
- Industrial Internet - information and communication infrastructure based on connecting industrial devices, equipment, transmitters, sensors, and process control systems, the data of which are integrated without human involvement;
- New materials - technologies for creating materials with an internal structure built in such a way as to correspond to a given set of functional properties.
2 Problems on implementing digital technologies in mechanical engineering
In mechanical engineering, digital technologies are implemented in modern equipment and production preparation technologies. Modern mechanical engineering technologies are expensive. For example, modern machining equipment has a high cost: a machining centre "DMU 125 duo BLOCK" costs more than 60 million roubles. The efficiency of using such equipment is conditioned by its utilisation.
The utilisation of equipment is limited, on the one hand, by the availability of control programs for machining parts, and on the other hand, the sufficiency of the production program available in the production division where modern equipment is installed. To utilize a modern manufacturing equipment unit, it is necessary to redistribute the production program of the enterprise between its structural subdivisions (workshops). Naturally, the redistribution of a production program will lead to a decrease in income for the personnel of the shops where the old equipment is installed, and will also violate social interaction between the units, which implies conflicts. Violation of social balance within the staff of an enterprise will make it difficult to retrain personnel for new technologies. As a result, it will have a negative impact on the economic efficiency of the entire production.
The authors carried out a study of a load of machining centres DMU in the first year after their introduction into operation at the machine-building enterprises of Primorsky Krai. A total of 7 units of equipment were studied. The results of the study are presented in Fig. 1.
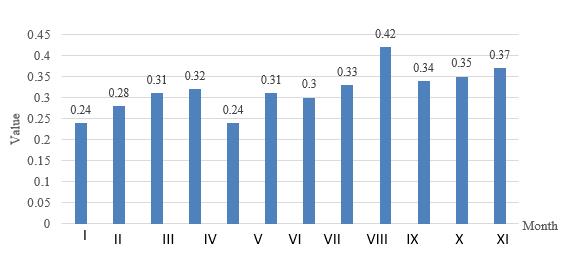
The average equipment utilization rate for the period under consideration was 0.32. Given the high cost of the equipment used, its low utilization rate leads to an increase in the cost of production, which negatively affects the performance of the enterprise.
The reasons for this situation were:
1) Insufficient number of developed control programs for machines;
2) The presence of errors in the control programs used, which required their correction;
3) Lack of tools and technological equipment;
4) The system of staff motivation, which did not encourage employees to increase their productivity.
The main reason for low equipment utilization was the lack of a sufficient number of control programs for the machining centres. The development of control programs requires certain competencies in programming and machine-building technology. When the new equipment was introduced, writing programs was entrusted to engineers-technologists, whose remuneration system did not encourage them to work productively.
In addition, when writing programs there were problems caused by the lack of coordination between the various structural subdivisions responsible for the preparation of production at the enterprise. There were cases when it was necessary to make corrections into a ready-made control program in connection with changes in product design. This required time for writing a new program and debugging it.
When writing a control program, a lot of time was also spent on searching for the necessary normative and reference information. This was because the new equipment was introduced into a production system, where the information and communication system of production preparation was not effective enough.
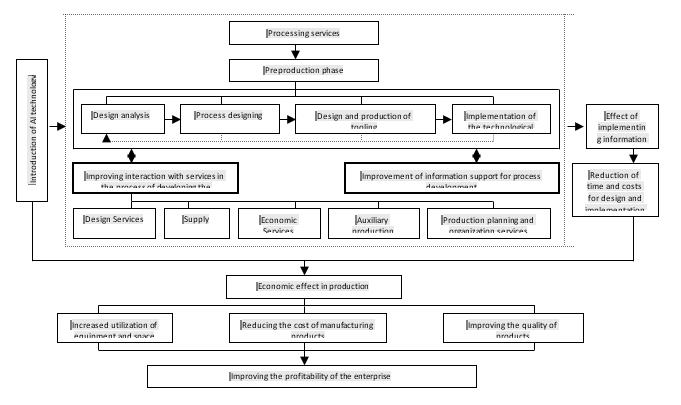
The role of modern information and communication technologies used in the preparation of production at a machine-building enterprise is shown in Figure 2.
Modern information and communication technologies make it possible to improve the interaction between structural subdivisions involved in production preparation. For example, the services that develop the control program will promptly make adjustments to the program, as they will be able to track changes in the product design in real-time. Also, modern information and communication technologies lead to the reduction of time for approval of various documents, which increases the speed of implementation of advanced technological processes.
The use of modern information and communication technologies improves information support of the production preparation process. Data and previously developed technological processes, control programs, available equipment, technological equipment, technical and economic standards are stored in a single database. Production engineers can use the information they need without spending a lot of time searching for it.
One of the reasons for low equipment utilization was a lack of tools. Special expensive tools are used for high-performance equipment. Due to errors in control programs and overestimation of machining modes by workers, tools often malfunctioned, which led to equipment downtime and extra time spent on searching for the right tool (10-15% of working time). In addition, tool shortages were caused by the fact that outdated standards were used in planning tool requirements.
Thus, it follows from the study that the introduction of modern equipment based on digital technology requires a comprehensive approach. Digitalization should cover not only production processes but also supporting processes, in particular production preparation processes. It is also necessary to work out the issues of employee labour organization and personnel motivation.
To remedy this situation, it was proposed:
- To change the personnel motivation system: the salary of control program developers should be linked to the quantity and quality of the implemented control programs;
- To create an information system for production preparation at enterprises based on modern information and communications technologies;
- To organize the centralized provision of workplaces with necessary tools. Calculation of tool requirements shall be made based on tool consumption research data.
As a result of implementing the suggested measures, there should be a decrease in the cost of production and an increase in labour productivity: production volume should increase by 62 %, the average cost per one part should decrease by 36 %.
Conclusion
It follows from the results of the study that the introduction of modern digital technologies, which have great potential to increase efficiency, should be comprehensive, covering also organizational and economic issues in addition to technical ones. Insufficient attention to the organizational and economic components at the initial stages of implementing those technologies leads to higher prices for new technology, requires additional costs, which ultimately has a negative impact on the economic efficiency of the implemented technology. In addition, advanced technologies should cover not only a separate main stage of the production process but the supporting processes as well. A comprehensive approach to the implementation of advanced digital technologies will improve the efficiency of technological modernization of domestic mechanical engineering.
Acknowledgments
This work was supported by the grant of the President of the Russian Federation №NS-2668-2020.6 "National-cultural and digital trends in the socio-economic and political-legal development of the Russian Federation in the XXI century"
References
Astakhova, E. V., Reshetnyak, E. I., & Ilchenko, V. V. (2019). The Analysis of Trends and the Assessment of the Worldwide High-Tech Production Development. IOP Conference Series: Earth and Environmental Science, 272, 32218.
Brovko, P. M., & Karastelev, B. Ya. (2021). Innovative tools for managing technological development of helicopter manufacturing in the Russian Far East. VSUES Publishing House.
Brovko, P. M., & Petruk, G. V. (2016). Strategic management in the development of military-industrial complex enterprises with the use of dual technologies under the resource-based approach. Economic and Social Changes: Facts, Trends, Forecast, 3(45), 82-97.
Brynolfson, E., & Makafi, E. (2017). Vtoraya era mashin [The second era of machines]. AST Publishers.
Christensen, C. M., & Overdorf, M. (2000). Meeting the challenge of disruptive change. Harvard Business Review, 78(2), 66-75.
Danchikov, E. A., Gureva, M. A., Polozhentseva, Y. S., Chernenko, E. M., & Varavenko, V. E. (2017). Problems of the development of Russian economy in the modern world. International Journal of Applied Business and Economic Research, 15, 83-90.
Fatkhutdinov, R. A. (2005). Organizaciya proizvodstva [Organization of production]. MOSCOW.
Fayol, A., Emerson, G., Taylor, F., & Ford, G. (1992). Management is a Science and Art. Respublika.
Ford, M. (2016). Robots are advancing. The development of technology and the future without work. Alpina non-fiction.
Furubotn, E. G., & Richter, R. (2005). Institutions and Economic Theory: Achievements of New Institutional Economic Theory. Saint Petersburg: Publishing House of St. Petersburg State University.
Glazyev, S. Y. (2010). Strategiya operezhayushchego razvitiya Rossii v usloviyah global'nogo krizisa [Strategy of advanced development of Russia in the conditions of global crisis]. Economics.
Kuzubov, A. A., Shashlo, N. V., Petruk, G. V., & Korostelev, A. A. (2018). Developing a supply chain subsystem to manage the process of obstacle elimination for the innovative development of business entities. International Journal of Supply Chain Management, 7, 621-631.
Novitsky, N. I. (2002). Organizaciya proizvodstva na predpriyatiyah [Organization of production at enterprises]. Moscow. Finance and Statistics. [in Russ.].
Odintsova, M. I. (2009). Institutional Economics. Publishing house of the State University Higher School of Economics.
Perez, C. (2011). Technological Revolutions and Financial Capital. Dynamics of Bubbles in the Period of Prosperity. Delo Publishing House RANE & GS.
Petruk, G. V., & Shashlo, N. V. (2019). Implementation of the Science Development Strategy: New and Non-Standard Solutions. Dilemas contemporaneos-educacion politica y valores. 7, 57
Petruk, G., & Vorozhbit, O. (2017). Strategic corporate management mechanisms: resource-market concept. Turkish online journal of design art and communication, 7, 1186-1195.
Shashlo, N. V., Osipov, V. A., & Kuzubov, A. A. (2019). Using conceptual models of added value to evaluate the efficiency of the activity of industrial enterprise structures. Dilemas contemporaneos-educacion politica y valores. 6(S6), 128.
Shashlo, N. V., Petruk, G. V., Korostelev, A. A. (2018). Determinants of integration interaction among the subjects of the entrepreneurial innovation ecosystem of macro region. Amazonia investiga, 7, 351-363.
Sokolitsyn, S. A., & Kuzin, B. I. (1988). Organizaciya i operativnoe upravlenie mashinostroitel'nym proizvodstvom [Organization and Operative Management of Machine-Building Production]. Leningrad: Mashinostroenie, Leningrad branch.
Sukharev, O. S. (2008). Economics of Technological Development. Moscow: Finance and Statistics.
Titova, N. Yu. (2020). Principles of circular economy introduction in Russian industry [Principios de introducción a la economía circular en la industria rusa]. Universidad y Sociedad, 12, 203-208.
Titova, N. Yu., & Terentyeva, T. V. (2020). Principles of circular economy introduction in Russian industry. Revista universidad y Sociedad, 12, 203-208.
Volkov, O. I., & Devyatkin, O.V. (2010). Organizaciya proizvodstva na predpriyatii (firme). [Organization of production at an enterprise (firm)]. INFRA-M.
Williamson, O. I. (1996). Economic institutions of capitalism: Firms, markets, "relational contracting". Lenizdat; CEV Press.
Womack, J. P. (2003). Lean thinking. Free press.
Yakubovsky, Y. V. (2006). Teoriya i praktika sovershenstvovaniya korporativnogo upravleniya [Theory and practice of corporate management improvement]. Problems of reforming and peculiarities of the Far East electric power industry development: materials of scientific-practical conference, 190-193.
Copyright information
This work is licensed under a Creative Commons Attribution-NonCommercial-NoDerivatives 4.0 International License.
About this article
Publication Date
03 June 2022
Article Doi
eBook ISBN
978-1-80296-125-6
Publisher
European Publisher
Volume
126
Print ISBN (optional)
-
Edition Number
1st Edition
Pages
1-1145
Subjects
Social sciences, education and psychology, technology and education, economics and law, interdisciplinary sciences
Cite this article as:
Brovko, P. M., & Petruk, G. V. (2022). Organizational Peculiarities Of Digital Technology Implementation In Production Processes. In N. G. Bogachenko (Ed.), AmurCon 2021: International Scientific Conference, vol 126. European Proceedings of Social and Behavioural Sciences (pp. 174-182). European Publisher. https://doi.org/10.15405/epsbs.2022.06.20