Abstract
Nowadays there are more than 170 enterprises working in electrical and electronics industry in Latvia. Ongoing expansion and increasing of production at the enterprises of Latvian electronic industry simultaneously increases the risk of harmful chemical exposure on employees of these enterprises, because of the volume and intensity of the use of health harmful chemicals increases. The aim of the article is to analyze the chemical safety of employees in the electronic industry enterprises. The analysis of the production process of electronic products has been done. It is noted that the basic chemical safety is associated with the processes of soldering electronic components. An analysis of the impact of production volumes on the concentration of harmful substances in the working area was done by the example of one of Latvian electronics industry enterprises. It is noted that the main measure eliminating the harmful effects of lead vapors is the ventilation system. The authors performed the calculation of the concentration of lead vapors in the work area taking into account the increasing production and defined the requirements for the ventilation system.
Keywords: Processsoldering of electronic componentschemical safetylead vapor concentrationventilation system
Introduction
At present time over 170 enterprises are operating in electric and electronics industry of Latvia. This sector of Latvian industry is rapidly developing, being one of most profitable branches of Latvian economy. To manufacture modern electronic devices, enterprises of this industry use up-to-date technologies and high-output equipment ensuring the automation of technological processes. At the same time, manufacture of electronic devices widely uses various chemicals that make a negative impact upon human health.
Ongoing extension of production and its growing volumes at enterprises of electronics industry in Latvia simultaneously increases the hazard of harmful chemical impact upon employees of these enterprises associated with increasing volumes and intensity of use of health-hazardous chemicals. Therefore, of topical urgency is the examination of chemical safety of personnel at enterprises of electronics industry and development of recommendations on improvement of labor conditions and health maintenance of this category of employees ("Occupational health and safety," 2007; "Occupational health," 2010; "Work safety," 2010; Kaļķis, 2001; “REACH,” 2014).
The purpose of the present article is to analyse the chemical safety of employees at enterprises of electronics industry.
Problem Statement
Enterprises of Latvian electronics industry manufacture electronic products by surface mount technology. Such technology provides the competitiveness of and demand for the manufactured electronic devices. These enterprises possess a unique and operatively convertible production base. Practically at all enterprises of electronics industry, the process is carried out on modern, fully automated process lines.
Generally, PCB surface mount process consists of the following phases: PCB inspection, application of soldering paste on PCB, automatic insertion of components, soldering, automatic optical inspection, repair of nonconforming products, gluing of components, manual insertion of components, application of silicon mask, selective or wave soldering, PCB cleaning from flux residues, lacquering and testing of products.
General process chart may be illustrated as follows (see Fig.
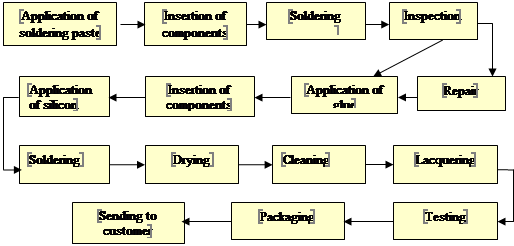
Labor safety regulations in production shops are determined by the nature of manufacturing process. Therefore, the labor safety measures in manufacture of electronic equipment have their own specificity (Komkin, 2007).
Specified microclimate parameters shall be provided at the workplace, which are corroborated by regulatory documents:
temperature (20-23)C at allowable values (19-25)C;
relative humidity (30-60%) at allowable value not exceeding 75%;
air velocity: ≤ 0.2m/s;
illumination (200-400) lx.
The biggest hazard for health of personnel is brought with the following electronic equipment manufacture processes: soldering of electronic components on PCB, gluing of components and lacquering of conducting surfaces and units for provision of high reliability standards of manufactured electronic equipment within wide range of temperature, humidity and other operational conditions ("Occupational health and safety," 2007; Kaļķis, 2001; Urbane, 2005).
Research Questions
The research questions of the paper are:
1. To analyse electronic equipment production processes.
2. To analyse electronic equipment production processes hazardous factors.
3. To analyse harmful substances concentration in working areas.
4. To analyse exhaust ventilation system at soldering places and its efficiency.
5. To estimate pressure losses in TE ventilation system air duct network.
6. To make a conclusions about air chemical safety of employees at enterprises of electronics industry.
Purpose of the Study
The purpose of the present article is to analyse the chemical safety of employees at enterprises of electronics industry.
Research Methods
Research methodology is based on literature review, as well as secondary statistical data and comparative analysis. The authors also use the general logical methods of deduction and induction, analyze the impact of production volumes on the concentration of harmful substances in the working area on the example of one of the Latvian electronics industry enterprises.
Findings
Electronic Equipment Production Processes and Hazardous Factors
Soldering of SMD components is carried out with the use of soldering pastes by heating in special devices (furnaces) while parameters of this process are set and controlled by a computing device. Soldering alloys and fluxes are used for soldering of components mounted in openings of the boards and for elimination of defects in automated soldering of SMD components. Composition of soldering alloys and fluxes includes lead with percentage that may exceed 50%.
Various phases of electronic equipment manufacture involve a wide use of lacquers, solvents, acids, mixtures and many other raw components potentially dangerous to health of personnel of enterprises.
Bonding of components is carried out by means of adhesives based on phenolformaldehyde, organo-siloxane and epoxy resins.
A characteristic feature of abovementioned processes is the emission of gaseous products making harmful impact upon personnel, dangerous for their health. In working environment, gaseous chemicals most often get into the body via respiratory tract and then via lungs get into blood circulatory system and are further spread throughout the body. Low level of labor hygiene, smoking during work (pollution with tobacco smoke, contamination of smokers’ fingers) and low level of personal hygiene may considerably increase the entire hazardous impact of chemicals upon health of personnel since their additional amount will get into the body orally (LVS 89, 2004).
The main hazard of lead is in its toxicity. Clinical lead poisoning is one of most heavy vocational disease. Lead hampers a normal functioning of cells and a number of physiological processes. The most sensitive target for lead poisoning is nervous system, which is manifested as minor behavioral changes, fatigue, reduced concentration and deterioration of motoric functions. Lead inhibits the body’s ability to produce hemoglobulin by several enzymatic steps in the heme exchange. Lead may cause two types of anemia. Acute poisoning with high lead doses causes hemolytic anemia. Lead also makes endocrinous impact, affects kidneys, reproductive function and development, as well as has cancer-inducing effect ("Occupational health," 2010).
Fluxes used in soldering also are toxic. Thus, colophony causes skin irritation and rash. Adhesives and lacquers are fire-hazardous and toxic, causing hand skin disease, irritation of respiratory tract, making adverse impact upon blood, blood-vascular organs and central nervous system (“Agency for Toxic Substances,” 2005).
Preventive measures against vocational poisoning at electronics industry enterprises include: hygienic rationalization of production process, its mechanization and hermetization. To prevent harmful impact, all soldering alloys, fluxes and other chemicals must be stored in a special tightly closed container.
A general measure, which eliminates the impact of harmful gaseous emissions at enterprises of electronics industry, is the use of local exhaust ventilation in addition to the centralized supply and exhaust ventilation. Soldering workplace is equipped with local exhaust ventilation ensuring the lead concentration in the working area not exceeding the maximum allowable value (0.01 mg/m3). Insulation stripping by firing is accompanied by smoke emission with a heavy and unpleasant odor. Therefore, upon firing of a large batch of wires, an exhaust hood with proper ventilation should be used. Work with paint-and-lacquer materials should only be carried out a separate room with supply and exhaust ventilation.
The efficiency criterion of ventilation systems is the reduction in concentrations of harmful substances in the air of the working area down to their maximum allowable values and lower. In this connection, the arrangement of the air ventilation system in the working area should meet the following requirements:
Capability of ventilation system should be sufficient to ensure necessary conditions in the working area.
Such air supply and exhaust methods should be used, which ensure the maximum efficiency of the working area air ventilation system.
Ventilation system should include the air filtering system.
In initial operation phase of an enterprise of electronics industry, arrangement and specifications of ventilation system fully meet these requirements. However, with growing volumes of production and extending working area the ventilation systems are modernized without consideration of quantitative indicators, such as concentration of health-hazardous substances in the air of the working area and necessary speed of air flow created by the ventilation system. At all enterprises of Latvian electronics industry, upon increasing production volumes the working area is extended by organization of additional workplaces and laying to them the air ducts branching from already used ventilation systems. Therefore, the analysis of changes in concentration of harmful substances in the working area and appearing requirements towards modernization of ventilation system were examined by example of a Latvian enterprise producing small-size electronic boards and modules for network and household electronic devices with the use of process illustrated by chart in Fig.
Analysis of Harmful Substances Concentration in Working Area Air
Laboratory measurements of harmful substances concentration in the air of the working area were regularly carried out since the time the production was started at the analyzed enterprise. Concentration of harmful substances in the air was identified by laboratory methods. Evaluation of chemical concentration in the air was carried out by comparison of its concentration with its normative
Laboratory monitoring of the air in the working area is carried out in regular production conditions, during the process in accordance with technological regulation of manufacture and the developed programme of operational control (“REACH,” 2014).
To monitor the chemical composition of the air in the working area, the air sampling was carried out within the worker’s respiration area, with maximal approaching of an air intake device thereto: at 1.5 m height from the floor at standing activity or at 1 m height at seating activity. Where a worker had no a permanent workplace, the air sampling was carried out in all spots of the working area where the worker appeared during its working shift.
Air sampling devices were placed both in fixed spots of the working area by the stationary method and by the personal monitoring method – the air sampler is attached directly at the worker’s clothing. Methods for monitoring of lead content in the air: in accordance with ISO 9855:1993: Work place air.
Air sampling is made by respiration via “Varian 3800” gas chromatograph. The measurement results of the last soldering step are presented in the table (see Table
* - expanded uncertainty indicated for average values is determined as mean-square deviation multiplied by overlapping coefficient 2, providing 95% reliability level.
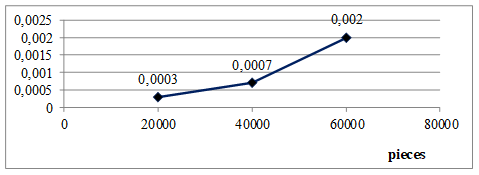
Growing lead concentration in the air of the working area is explained by increased number of soldering places (currently 7) as well as increased number of soldering operations.
Monitoring of air chemical composition in the working area allows to obtain an objective picture of lead concentration and its changes in the result of output expansion. However, monitoring of air chemical composition in the working area by sampling is a costly inoperative measure carried out with intervals of several years. In case of expanded production and increased number ow workplaces, the results of monitoring of air chemical composition in the working area are a late confirmation of increased concentration of harmful substances, lead in this case, in the working area. Consequently, modernization or replacement of currently employed exhaust ventilation system, which does not provide necessary air purity at current conditions and volumes of production, will be also belated.
Use of automated ventilation systems at enterprises of Latvian electronics industry would provide the required concentrations of harmful substances, including lead, in the working area. However, installation of such automated ventilation systems requires additional expenses and therefor they are not used at enterprises of Latvian electronics industry.
As a consequence, at present time in the Republic of Latvia the monitoring of air chemical composition in the working area by air sampling is the basic method allowing to identify the necessity and degree of modernization of ventilation systems at any industrial enterprises. Therefore, of urgency is the efficiency analysis of exhaust ventilation systems upon growing number of workplaces and production volumes (number of soldering operations). Operative modernization of exhaust ventilation system in accordance with estimated technical parameters will provide a timely health protection of personnel within the working area against impact of lead and other harmful substances typical for electronics production.
Efficiency Analysis of Exhaust Ventilation System at Soldering Places
Efficiency analysis of exhaust ventilation systems at soldering places was carried out for production conditions and facilities of such enterprise where the air of the working area demonstrated the growth in lead concentration as a result of increased number of soldering places and output of electronic products (Table
At one workplace one worker performs soldering with soldering allow NAC 60/40 at output rate N = 100 contact per hour. Lead-tin soldering alloy NAC 60/40 contains С = 0.4 parts of lead volume and 60% of tin. The most poisonous are lead sprays (vapors) (Alexeeff et.al., 1999). During the soldering process, up to B = 0.1% is evaporated from the soldering alloy while 1 soldering requires m = 10 mg of soldering allo. The amount of lead sprays emitted into the air:
G = c * B * m * N. /100 = 0.4 mg/h(1)
The required air exchange at emission of harmful substances is determined by:
L = G * 1000/(XT – XA) = 44.45 m3/h (2)
where:L, m3/h – required air exchange;
G, g/h – amount of harmful substances emitted into the air (1);
XT,= 0.01 mg/m3 – maximum allowable harmful concentration in the air of the working area of a premise;
XA = 0.001 mg/m3 – maximum allowable the same harmful concentration in the air of populated locations.
Total output rate of local exhaust system, which is used for air exhaust from soldering places and from equipment installation places, TE (Technological Exhaust) Ln = 1000 m3/h.
The number of workplaces in the soldering section is 7, thus the required air exchange for the whole soldering section:
L7=7* L1=7*44.45 m3/h = 311.15 m3/h
TE exhaust system has also thereto connected microwave oven Wave Soldering Seho, which in accordance with technical documentation of the oven requires the air exhaust 500 m3/h from the oven.
Thus, TE exhaust system should have output rate equal to:
WN = Kk (L7+500)
where Kk = 1,3..2,0 – reserve coefficient. Choosing the average reserve coefficient, we determine TE exhaust system should have output rate:
WN=1.7*811.15 =1,378.955 m3/h
Diagram of TE exhaust ventilation system is shown on Fig.
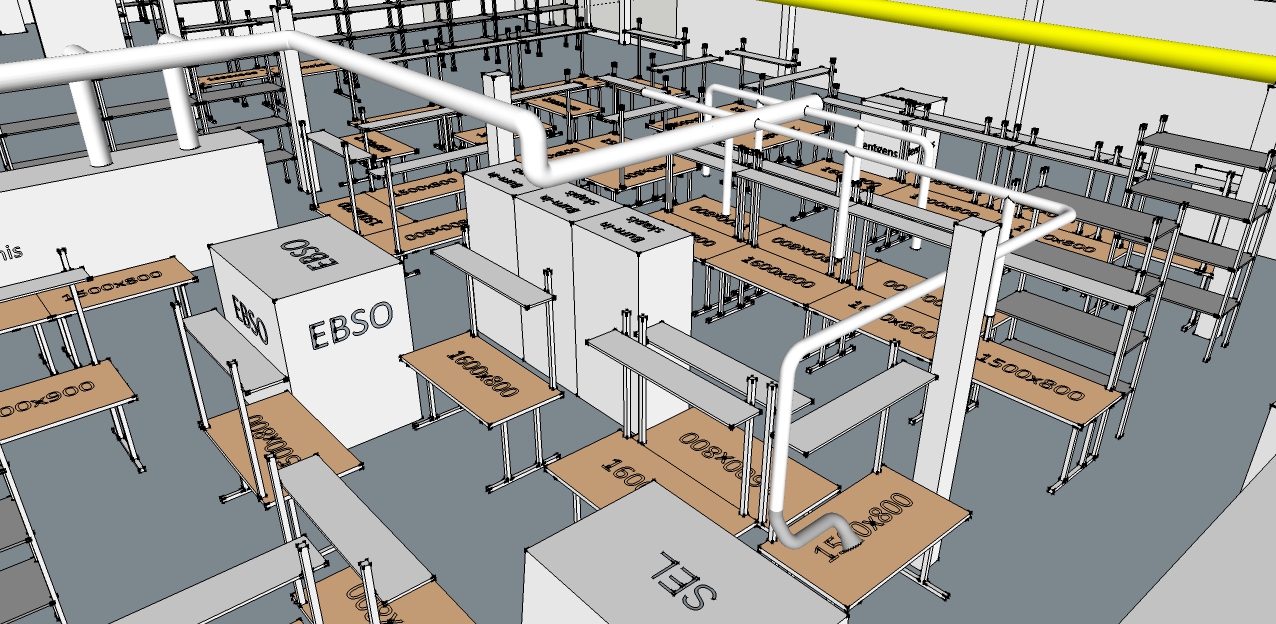
Air duct of ventilation system consists of 10 straight-line sections. Using the length and diameters of straight air duct pipes and air velocity at these sections, total pressure losses in the air duct network were calculated by formula (Petrov, Volhin & Petrova, 2006):
(3)
where Ri – abrasion pressure losses at estimate i-section of air duct (Pa) per 1 m;
li - length of i-section of air duct, m;
zi – local resistance pressure losses at estimate i-section of air duct, Pa.
Abrasion pressure losses Ri, Pa/m, in round air ducts are determined by formula (4)
,(4)
where λi – abrasive resistance coefficient at i-section of air duct;
di – diameter of i-section of air duct, m;
Vi – air velocity at i-section of air duct, m/s;
ρ – density of air moving in air duct, is equal to 1.2 kg/m3;
ρV2/2 – velocity (dynamic) pressure, Pa.
Abrasive resistance coefficient is calculated by Altschul formula (5):
(5)
where Кa – absolute surface roughness of steel plate air duct Кe = 0.1 mm;
di – diameter of air duct, mm;
Rei – Reynolds number for i-section of air duct.
Reynolds number is a nondimensional characteristic of liquid flow, which is determined by proportion between dynamic pressure (ρv2) and contact tension (μv/L) and calculated in the following way:
(6)
where Re – nondimensional Reynolds number;
ρ – air density, which is equal to 1.2 kg/m3;
Vi – air velocity at i-section of air duct, m/s;
μ – dynamic air viscosity, which is equal to 0.00185 Н*s/m2;
di – diameter of i-section of air duct, m.
Pressure losses on local resistance zi, measured in Pa, with bends and elements of the air duct structure: grilles, valves, manifolds, etc. Local resistance in TE1 exhaust ventilation system is created by the bends in all sections except sections
(7)
where kp – local resistance coefficient at i-section of air duct, with air duct bend angle equal to 900.
Vi – air velocity at i-section of air duct, m/s;
ρ – density of air moved via air duct, which is equal to 1.2 kg/m3.
Total pressure losses in TE1 air duct network are determined in Microsoft Excel (see Table
Losses for the last section (N=10) were determined with consideration of all eleven soldering workplaces.
po = 1.184
mu = 0.0000185
Thus, total pressure losses in in TE ventilation system air duct network are H = 344.62 Pa.
Therefore, TE system fan should ensure compensation for pressure losses 344.68 Pa in the air duct network. However, fan used in the exhaust system in accordance with technical documentation creates the initial air pressure in the air duct network, which is equal to 290 Pa.
Conclusion
Main findings of the studies:
Analysis is performed of modern processes in manufacture of electronic products (devices) and identification of factors harmful for health of employees. It is demonstrated that lead soldering and application of lacquer on the products are the main source of air pollution in working environment.
The results of monitoring of chemical composition of the air in the working area by sampling method have established a tendency of growing lead concentration in the air of the working area with increasing output of electronic products. This tendency is specific to all enterprises of Latvian electronics industry due to similarity of production organization, employed process equipment and exhaust ventilation systems.
The necessity is substantiated to perform the efficiency analysis of exhaust ventilation systems in the working area of electronics industry enterprises upon increasing number of soldering places and production volumes since the monitoring of chemical composition of the air in the working area by sampling method does not allow to operatively identify the requirements to modernization of exhaust ventilation systems in the working area.
The efficiency analysis has been performed of exhaust ventilation system at soldering places of electronics industry enterprise, demonstrating the growth in lead concentration in the air with increasing number of soldering places and production volumes. Based on the results of calculations, specifications have been identified for modernization of exhaust ventilation at this enterprise.
The proposed approach to the efficiency analysis of exhaust ventilation system at soldering places may be used at other enterprises of Latvian electronics industry.
At the same time, it is necessary to carry out a continuous monitoring of air composition in the working area in order to identify the impact of increased production volumes on concentration of harmful substances and the need for identification of required parameters of exhaust ventilation system at soldering places.
References
- Agency for Toxic Substances and Disease Registry (ATSDR) (2005). Minimal Risk Level (MRL) for Hazardous Substances.
- Alexeeff, G.V., Budroe J.D., Collins J.F., Lam R., Lewis D.C., Lipsett M.J., Marty M.A., Parker T.R. (1999). Air toxics HOT Spots Program Risk Assessment Guidelines. Part I. The Determination of Acute Reference Exposure Levels for Airborne Toxicants. California environmental protection agency office of environmental health hazard assessment air toxicology and epidemiology section. March. 1999. p 71.
- Dzīvojamo un publisko ēku apkure un ventilācija (2003). LR MK noteikumi Nr. 534 (23.09.2003.). Latvijas būvnormatīvs LBN 231-03 / likums [Elektroniskais resurss]/NAIS – Resurss apskatīts 2014. gada 17.janvārī.
- Kaļķis, V. (2001). Occupational risk factors and workers' health protection (Darba vides riska faktori un strādājošo veselības aizsardzība) /Ž.Roja, M. Eglīte etc al. – Rīga: Elpa, p. 500. (In Latvian).
- Komkin, A.I. (2007). Calculation of mechanical ventilation systems (Raschet system mehanicheskoi ventilyacii. Uchebnoje posobije). Moscow: MGTU Baumana, p.185. (In Russian)
- LVS 89 (2004). Occupational Exposure Limit Values of Chemical Substances in Work Environment (Ķīmisko vielu aroda ekspozīcijas robežvērtības darba vides gaisā), Riga: Latvijas standarts, p 62. (in Latvian)
- Occupational health and safety requirements for exposure to chemicals in the workplace. LR Cabinet Regulations Nr.325 (Darba aizsardzības prasības saskarē ar ķīmiskajām vielām darba vietās: LR MK noteikumi Nr. 325 (In Latvian). (2007, May 15). Retrieved from http://likumi.lv/doc.php?id=157382.
- Occupational health. Ministry of Welfare (Darba drošība (2010). LR Labklājības ministrija), p. 180. (In Latvian). (2010). Retrieved from http://www.lbas.lv/upload/stuff/201103/darbahigiena.pdf
- Occupational Lead Exposure: Information for Physicians. (2004, April 30). Retrieved from www.lrws.gov.sk.ca/occupational-lead-exposure-information-physicians
- Petrov, S. V., Volhin, S. N. & Petrova, M. S. (2006). Occupational safety in the workplace and in the learning process (Okhrana truda na proizvodstve i v uchebnom processe. Uchebnoje posobiye). Moscow: ENAS, p.232. (In Russian)
- REACH- Registration, Evaluation, Authorisation and Restriction of Chemicals. (2014). Retrieved from http://ec.europa.eu/enterprise/reach/index_en.htm.
- Urbane, V. (2005). Dangerous substances application security (Bīstamo vielu pielietošanas drošība) S.Lavendele. Rīga: RTU Izdevniecība, p.186. (In Latvian).
- Work safety. Ministry of Welfare (Darba drošība (2010). LR Labklājības ministrija), p. 280. (In Latvian). (2010). Retrieved from http://osha.lv/lv/publications/gramatas-2011/darbadrosiba.pdf
Copyright information
This work is licensed under a Creative Commons Attribution-NonCommercial-NoDerivatives 4.0 International License.
About this article
Publication Date
30 July 2017
Article Doi
eBook ISBN
978-1-80296-026-6
Publisher
Future Academy
Volume
27
Print ISBN (optional)
-
Edition Number
1st Edition
Pages
1-893
Subjects
Teacher training, teaching, teaching skills, teaching techniques,moral purpose of education, social purpose of education, counselling psychology
Cite this article as:
Urbane, V., Tambovceva, T., & Ievins, J. (2017). Determination Of Requirements For Ventilation System In Manufacturing Of Electronic Products. In A. Sandu, T. Ciulei, & A. Frunza (Eds.), Multidimensional Education and Professional Development: Ethical Values, vol 27. European Proceedings of Social and Behavioural Sciences (pp. 820-830). Future Academy. https://doi.org/10.15405/epsbs.2017.07.03.97